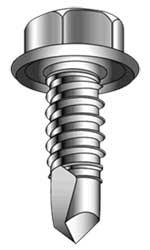
In the world of fasteners, steel thread-rolling screws have a distinct advantage thanks to their cold-forging production process. This leaves behind no swarf, significantly reducing the chances of damaging the composition of the plastic, including Ultem, during installation. They are tailor-made for plastic assembly, enhancing joint performance and assembly efficiency. Despite these benefits, the steel thread-rolling screw for plastic is often underutilized, overlooked in favor of conventional screws or fasteners, but not anymore.
Let’s explore why these unassuming screws are gaining popularity.
1. Increased Thread Engagement
Thread engagement is crucial for the strength of a connection, especially in plastic materials, which may not have the same resilience as metals. The unique thread design and rolling process of these screws allow for deeper and more consistent thread engagement in the plastic substrate. This means a stronger grip and less chance of pullout. As a result, your assemblies can withstand greater forces and maintain their integrity.
2. Reduced Risk of Stripping
We’re all familiar with the frustration of a stripped screw, but in the context of plastic materials, the stakes are even higher. Stripping a thread in plastic can compromise the integrity of the material itself, rendering the fastening point virtually useless. This is where a high quality steel thread-rolling screw for plastic shines.
3. Improved Load Distribution
Steel thread-rolling screws feature a thread design that improves load distribution within the plastic. The threads of these screws are asymmetrical, with a larger contact area on one side, which helps to spread the load more evenly when tightened. This even distribution reduces the risk of over-stressing a specific area of the plastic, which can lead to cracks or other damage.
4. Enhanced Resistance to Loosening
The unique thread design of steel thread-rolling sizescrews also provides a natural defense against loosening. The asymmetrical nature of the thread means that the screw is engineered to resist forces that might otherwise cause it to back out over time. This is particularly beneficial in applications subject to vibration, where conventional screws could work themselves loose, compromising the joint.